Sit on a knit

Displayed at the Dutch Design Week 2023, at the 4TU exhibition.
Textiles
surround us all. Typically, textiles are manufactured in large panels through
weaving or knitting, then cut and sewn together to make our garments. Knitting,
particularly 3D knitting on an industrial machine, can shape directly, thus
saving material and reducing labour.
Knitting allows for a wide range of material properties and aesthetics and can be integrated with other stiffer materials. The lightweight nature of the knitted fabric, combined with a structural material, allows for the development of easily transportable, large-scale objects while maintaining the advantages of 3D knitting.
How does 3D knitting
Knitting allows for a wide range of material properties and aesthetics and can be integrated with other stiffer materials. The lightweight nature of the knitted fabric, combined with a structural material, allows for the development of easily transportable, large-scale objects while maintaining the advantages of 3D knitting.
How does 3D knitting
redefine object-making?
Form follows material
The
project objective is to explore the opportunities and limitations of 3D
knitting through the design of a chair.
The research followed a Material Driven Design approach, meaning the design of
the chair stems from the discovered characteristics of knitting through sample
making and reflecting. Form follows material.
Textile Hybrid Chair
|

The chair shows we can rethink
current textile production methods to design lightweight, adaptable in
material properties, deployable, industrially produced, large scale objects,
minimizing the material waste and labour intensity. The chair is a textile-hybrid structure in which the tension of bent tubes balances the stretchable knitted textile. |
Deployment and reconfiguration
The chair deploys by releasing the attachments of the two overlapping panels. Reconfiguring the panels results in eight different aesthetics.
The colours and material expression are adaptable to the user needs and wishes.

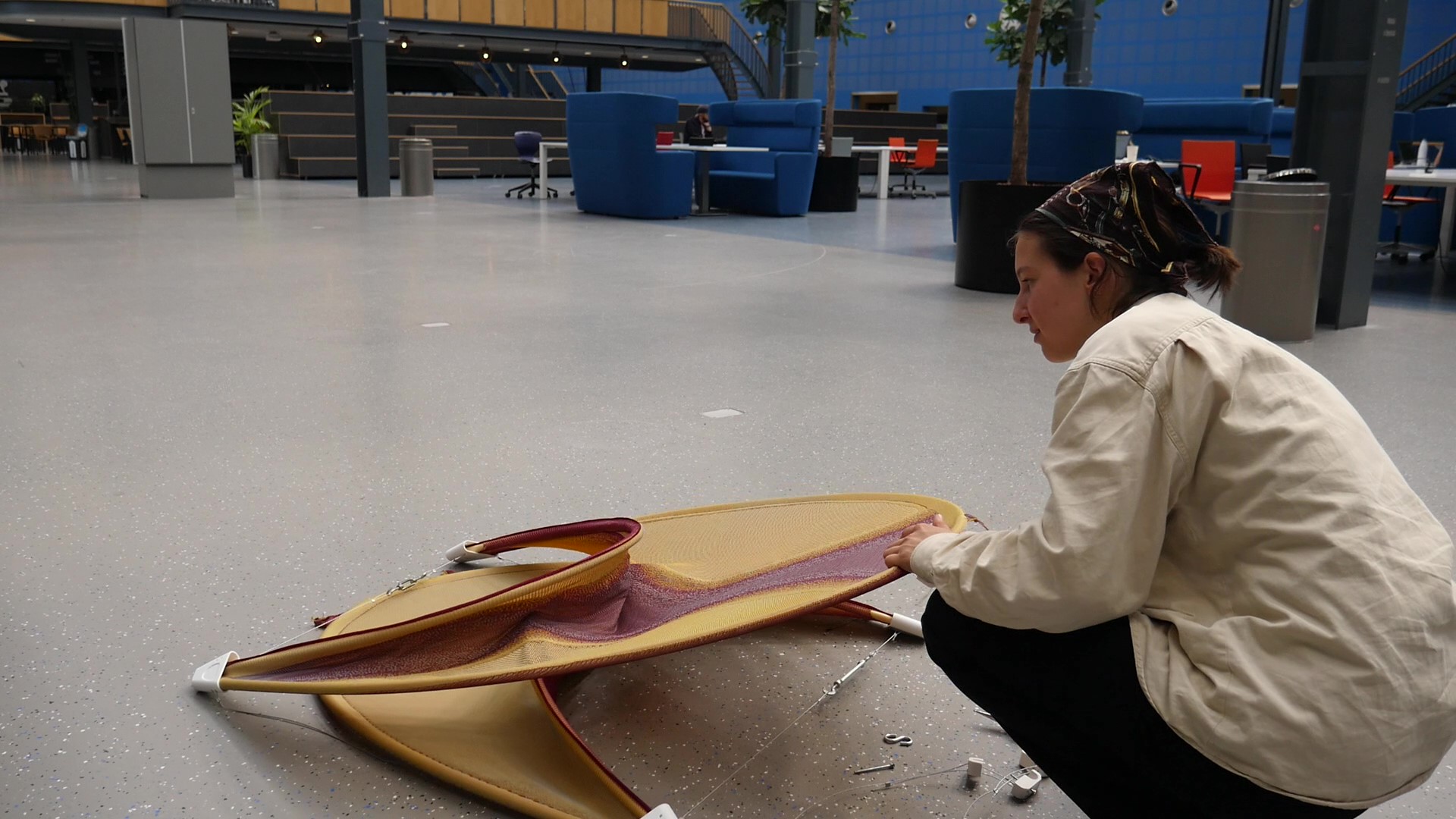

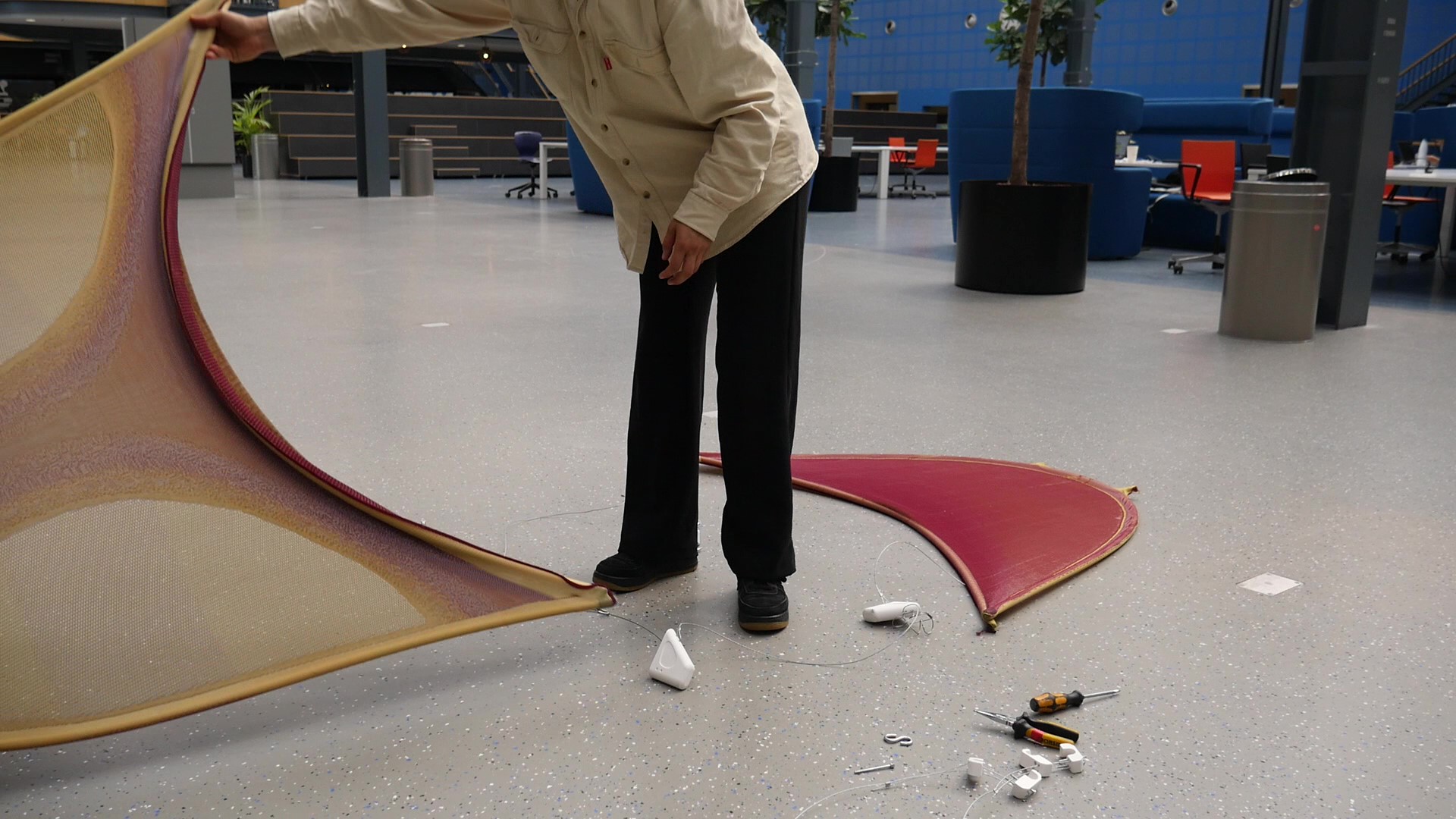



For the lastest version, designed and produced specially for the Dutch Design Week 2023.
Future research objectives
More in-depth research is required into the behaviour of 3D knitted textile-hybrid structures, which cannot be predicted through computational modelling yet because of the complex physics of the yarn material, loop formation and internal frictions. The development of textile-hybrid objects is thus a process of trial-and-error. Research into modelling of 3D knitted textiles can broaden the range of opportunities to utilize the method for large scale objects, and reduce the material usage and streamline the production process. |
Next page